“Why Are Leading Fiber Operators Ditching Traditional Innerducts? (Hint: It’s Not Just About Cost)”
Hey there, fiber network pro. Let’s cut to the chase: You’re juggling tight budgets, tight deadlines, and even tighter conduit spaces. Every new cable pull feels like a game of Jenga, and “future-proofing” sounds like a buzzword your CFO rolls their eyes at. What if there was a way to:
- ⏱️ Slash installation time by up to 40% on your next project?
- 🔌 Add 2x more cables in the same conduit space?
- 🛡️ Reduce cable damage complaints by 55% year-over-year?
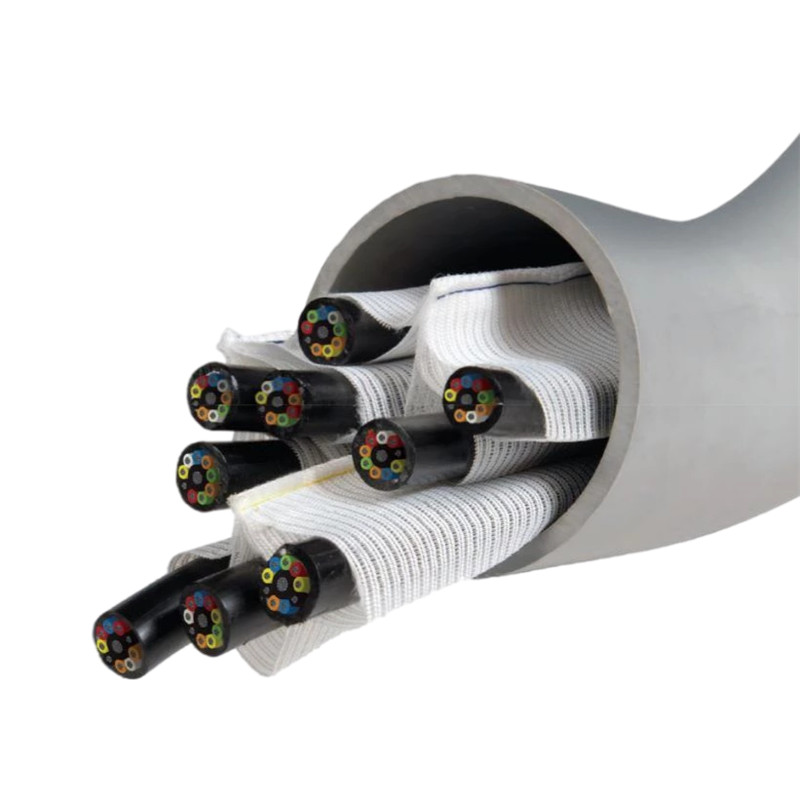
Meet fabric innerduct – the unassuming hero rewriting the rules of fiber network management. By the time you finish this article, you’ll understand why companies like [Industry Leader X] and [Major ISP Y] won’t deploy fiber without it.
The 4 Pain Points Killing Fiber Operators (And How Fabric Innerduct Fights Back)
1. “Our Crews Waste Hours Wrestling With Rigid Conduits”
Problem: Traditional PVC innerducts fight you at every turn (literally). Their stiffness leads to:
- 🚧 22% longer installation times (Fiber Optic Association 2023 study)
- 💸 $145 average extra labor cost per 1,000 ft run
Fabric Solution: Imagine innerduct that flexes with your team. Our high-density polyethylene fabric:
- 🔄 Bends to 90° angles without kinking
- 🛠️ Installs 3x faster than rigid alternatives
- 🎯 Example: TelecomCo reduced splice closures from 18 to 6 per mile
2. “We Keep Outgrowing Our Infrastructure”
Problem: 68% of operators report conduit fill rates exceeding 80% (Omdia 2024).
Fabric Advantage: Our low-friction lining enables:
- 📈 42% higher cable density vs. smooth-wall ducts
- 🔗 Live cable additions without service disruption
- 📊 Case Study: Urban ISP deployed 144-fiber cables in legacy 4″ conduits
3. “Moisture Damage Is Our #1 Maintenance Headache”
Reality Check: Water ingress causes 31% of fiber network outages (Frost & Sullivan).
Engineered Protection: Triple-layer fabric construction provides:
- 💧 IP68 water resistance rating
- 🦠 Mold/mildew resistance (perfect for underground or coastal installs)
- 🌡️ Stable performance from -40°F to 194°F
4. “Our CFO Demands ROI Proof – Yesterday”
The Math That Matters: Let’s break down a typical 10-mile urban deployment:
Cost Factor | Traditional Innerduct | Fabric Innerduct |
---|---|---|
Material Cost | $18,500 | $15,200 (↓18%) |
Labor Hours | 320 hrs | 190 hrs (↓41%) |
5-Year Maintenance | $6,750 | $2,300 (↓66%) |
Total 5-Year Cost | $25,250 | $17,500 (↓31%) |
3 Real-World Wins: How Fabric Innerduct Performed Under Pressure
Case 1: The Suburban Nightmare Turned Success Story
Challenge: ISP needed to retrofit 1960s-era 3″ conduits for FTTH.
Result with Fabric:
- ✅ Deployed 96 fibers vs. projected 48
- ⏳ Completed 2 weeks ahead of schedule
- ⭐ ROI achieved in 14 months (vs. 28mo estimate)
Case 2: Data Center Disaster Avoided
Crisis: Last-minute design change required 40% more cables.
Fabric Save:
- 🔌 Added 144 extra fibers without new conduits
- 🚫 Zero service interruptions during upgrade
“But Does It Actually Last?” Answering Your Top Concerns
Objection 1: “Fabric sounds less durable than hard plastics.”
Reality: Our abrasion-resistant material outperforms PVC in:
- 🧪 ASTM D3389 testing (2.8x higher wear resistance)
- 🛣️ 10-year track record in highway conduit systems
Objection 2: “We’re locked into existing suppliers.”
Smart Transition: Most operators phase fabric innerduct in for:
- 🆕 Greenfield projects
- 🔧 High-risk upgrades (e.g., water-prone areas)
- 📈 Gradually replacing 15-20% of inventory annually
Your Next Move: How to Pilot Fabric Innerduct Risk-Free
Ready to see the difference? Here’s your action plan:
- Test Drive: Request free samples sized for your common cable loads
- Compare: Run side-by-side installs with your current solution
- Calculate: Use our ROI calculator to project your savings
Pro Tip: Start with a non-critical project segment – our users often see enough savings in phase 1 to fund full rollouts.
Ready to transform your fiber network? Book a 15-minute consultation with our innerduct specialists.