Fiber optic splicing, especially fusion splicing, has become increasingly important for OSP (outside plant) deployment. The process is by joining the two fiber ends to create longer cable runs. As we know, spliced bare fibers are fragile to be easily breakable. Therefore, a good protection for the spliced fibers during fiber optic splicing is extremely necessary. Luckily, a small component named fiber protection sleeve perfectly solves the issue. It acts like a strong coat for the fiber splices to prevent unpredictable fractures. This post will take you to understand the basic knowledge about fiber protection sleeve.
Construction of Fiber Protection Sleeve
Generally speaking, a fiber protection sleeve consists three parts. The first part is the inner tube made by hot-meltable adhesive. This material can encapsulates the fusion splice joint and provides vibration damping and an environmental seal so as to protect the fiber from damage and contaminants. The second part is a reinforcing strength member outside the inner tube. The strength member can be made of stainless steel, ceramic or non-metallic. It offers extra rigidity to prevent misalignment, micro bending or breakage of the fiber. The third part is the heat-shrinkable outer tube made of cross-linked polyolefin. This tube provides an instant shrink-force and drives the adhesive liner into all areas of the splice and excludes all the air. The following picture shows the structure of a fiber protection sleeve.
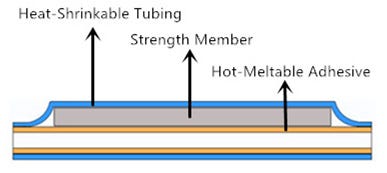
How Does It Work?
When the fibers are melt during the fusion splicing, technician will use the sleeve on the melt point as a protection. Once the hot-meltable adhesive tube touches the melted fiber, it also melts to tightly wrap the fiber joint for the filling and sealing functions. Likewise, when the heat-shrinkable tube is heated, it shrinks to wrap the fiber joint, strength member and hot-meltable tube to form a unity preventing moisture and increasing fiber joint’s strength.
Two Types of Fiber Protection Sleeve
Single Fiber Protection Sleeve
This kind of protection sleeve is used for single fibers. Its strength member adopts the stainless steel needles to reduce fiber damage. Typical lengths are 40 mm and 60 mm. The sleeve color is selective, but most people would choose the transparent tube for better inspection of the fiber status.
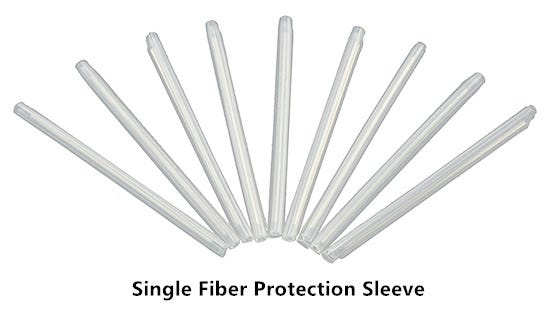
Ribbon Fiber Protection Sleeve
The ribbon type is to protect ribbon splices of multiple fiber counts. Ceramic strength member is used to support the splices. Fiber counts in a ribbon sleeve vary from 2 to 12 fibers. The length of the sleeve is usually 40 mm. If stronger protection is required, you can choose the ribbon protection sleeves with double ceramic strength members.
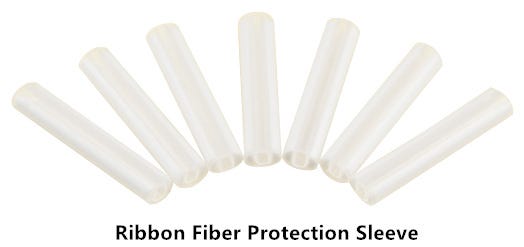
Be Aware of These Precautions
While utilizing the fiber protection sleeves, there are some important precautions for operators to know. The benefits of the precautions are about avoiding unnecessary loss and securing the fiber for a long-term use.
- Point 1, do not leave air bubbles in the protection tube. This ensures the long-term reliability of the fiber splices.
- Point 2, the tension applied to the fiber should be uniform so that the fiber can stay straight in the protective sleeve.
- Point 3, the tension applied to the fiber should not be too large in case fiber cracks increase.
- Point 4, try to avoid fiber twisting. Because this may cause micro-bending and unnecessary fiber loss.
- Point 5, do not release the tension until the heat-shrinkable tube is completely shrunk, cooled and shaped. This can avoid the uneven heating which leads to fiber bending.
Conclusion
Fiber optic protection sleeve is usually used during the process of fiber optic splicing. Although the sleeve is very small, it provides great support for the fiber joint. Single fiber protection sleeve and ribbon fiber protection sleeve are two common types in the market. All the above are available in BATIV.COM.